This may seem like a strange time of year to be thinking about winter pursuits but my studies have me too busy to even day dream about grand adventures let alone work on equipment. This past weekend I completed another pulk. This is the fourth version that I've made, the first was made of a 3 foot toboggan. It had molded in runners which was nice for anyone that was skiing behind me because the runners were spaced far enough apart to set a fairly decent track. The problem with it was that it was too small and I had to wear a 30 L backpack in order to bring enough gear. My second version was a 5 foot toboggan which proved to be wide enough to keep from tipping over but still not enough space. The third version was the same 5 foot sled with another attached to the top which opened like a clam shell. I had just enough room to fit gear and food for a weekend trip but anything longer than a couple of nights and I wouldn't have space and would have to resort to using a backpack again. All four pulks use a ridged pole system that is made of metal electrical conduit with swiveling brackets at the pulk end and a clasp that attached to my harness. My goal is to eventually go on extended winter camping trips that are two or three weeks in length. A friend and fellow winter camper, Bryan Saurer, even suggested a fly in trip. In order to bring enough gear for an extended trip I will need a bigger pulk which is why I build a fourth. This one measures 16" X 8' and has a 7" up-turn on the front end and weighs 21 lbs (which is more than I'd like but the supper slippery sliding surface will make up for it, at least that's what I tell myself). The sliding surface is a piece of UHMW polyethylene plastic, 1/4" thick. This material is nearly friction free on snow. In February, on a snowshoe trip to Nistowiak Falls, Bryan and I traded pulks for a while, I pulled his 10' sled which was loaded with 140 lbs of gear and he pulled my 5 foot pulk loaded with only 50 lbs. Bryan's pulled better, even with nearly three times as much weight! I was convinced at that point that I had to build a new a better pulk of my own.
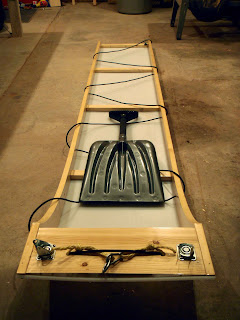